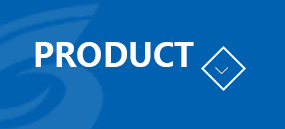
The planetary mixer is a new type of fast and dead point free mixing and stirring equipment, which has a special and innovative mixing form. There are two or three multi-layer blade mixers and 1-2 automatic bottom scraping and wall scraping knives in the kettle. The mixer rotates around the axis of the kettle body while also rotating around its own axis at different speeds, causing the material to undergo complex movements inside the kettle and subjected to strong cutting and rubbing. The scraping knife inside the equipment rotates around the axis of the kettle body, scraping the materials stuck on the wall to participate in mixing, making its effect more ideal.
The inner wall of the planetary mixer cylinder body (barrel) is finely processed by a large vertical lathe, and then automatically polished by a large polishing machine to ensure that the movable scraper on the planetary frame completely scrapes off the material on the inner wall of the cylinder body when rotating; This machine is particularly suitable for dissolving, mixing, mixing, and polymerizing paste, high viscosity, and high materials. The barrel body adopts a special sealing structure, which can be pressurized and vacuumed, and has a good exhaust and defoaming effect.
(1)Main supporting components:
One main machine of the planetary mixer (mixer), one hydraulic discharge machine (optional, large capacity not equipped), two material cylinders, one high viscosity gear discharge pump (optional), one vacuum pump (optional), two control cabinets (independent control of mixer and press), and two hydraulic stations.
(2)Product mix:
a. Structural forms: Gantry style, single arm style.
b. Cylinder head and power system: mainly for the power part, including one three-phase asynchronous motor, one reducer, transmission gear components for frame and planetary motion, sealing device, temperature measuring probe, sight lamp, window, vacuum tube mouth, observation port, and vacuum pressure gauge.
c. Cylinder body: The contact material part is made of stainless steel material welded and machined, with a plunger discharge port at the bottom, 4 casters, positioning guide rails, and a fixed locking device installed outside the cylinder body.
d. Base: welded structure.
e.Mixing system: 2-3 mixing blades with bottom scraping, generally including multi-layer folding type, Fried Dough Twists type and frame type. There is a scraper for scraping edges.
f. Hydraulic lifting system: composed of oil cylinder, oil pump, electric motor, pressure gauge, solenoid valve, shut-off valve, pipe fittings, and oil circuit control system.
g. Electrical control operating system: The operation and control of various mechanisms of the entire equipment can be achieved through two options: button or touch screen operation.
h. Vacuum system: connected to the vacuum buffer tank and pipeline, connected to the vacuum group; can play a role in dehydration, defoaming, deodorization, and other functions.
i. Discharge method: Optional hydraulic discharge machine can be used to press out from the top or high viscosity gear pump can be used to extract from the bottom discharge port. The pump can be used for material reflux circulation.
j. Other systems: Depending on the needs of different material processes, condensation devices or other devices can also be installed.