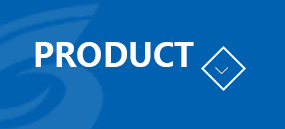
High Speed Dispersion Machine is a fast mixer that is widely used in various industries, has good sealing, can be vacuumed, has good defoaming effect, has no dead corners in mixing, combines high and low speeds, and is a mixing and stirring equipment that can fully and quickly disperse.
High Speed Dispersion Machine has three power driven electric motors, and there are three different forms of agitators inside the kettle, one low-speed wall scraping and bottom scraping agitator, and two high-speed disperser agitators. Two high-speed dispersion mixing devices rotate at different speeds around their own axes at high speeds. The rotor of the serrated circular dispersion disk can reach a linear speed of over 23m/s. Through the high-speed operation of the dispersion disk, the material undergoes complex movements in the cylinder, undergoing high-speed and intense shearing, impact, crushing, and dispersion, achieving the functions of rapid mixing, dissolution, dispersion, refinement, and emulsification; The low-speed mountain shaped street knife agitator rotates around the axis of the kettle body to discharge the raw materials stuck to the wall and bottom; It is a stirring and mixing equipment that combines high and low speeds without dead corners, and disperses thoroughly and quickly.
Main supporting components:
One main machine of the strong dispersing machine (mixer), one hydraulic discharge machine (optional, large capacity not equipped), two material cylinders, one high viscosity gear discharge pump (optional), one vacuum pump (optional), two control cabinets (independent control of mixer and press), and two hydraulic stations.
a. Gantry style, single arm style.
b. Cylinder head and power system: mainly for the power part, including 3 three-phase asynchronous motors, 1 reducer, frame and transmission part, sealing device, temperature measuring probe, sight lamp, window, vacuum tube mouth, observation port, and vacuum pressure gauge.
c. Cylinder body: The contact material part is made of stainless steel material welded and machined, with a plunger discharge port at the bottom, 4 casters, positioning guide rails, and a fixed locking device installed outside the cylinder body.
d. Base: welded structure.
e. Disperse mixing system: three mixers, one mountain shaped stirrer with scraping edges and bottom, and two high-speed dispersion shearers (generally using butterfly+dispersion plate, multi-layer dispersion plate as two sets)
f. Hydraulic lifting system: composed of oil cylinder, oil pump, electric motor, pressure gauge, solenoid valve, shut-off valve, pipe fittings, and oil circuit control system.
g. Electrical control operating system: The operation and control of various mechanisms of the entire equipment can be achieved through two options: button or touch screen operation.
h. Vacuum system: connected to the vacuum buffer tank and pipeline, connected to the vacuum group: can play a role in dehydration, defoaming, deodorization, and other functions.
i. Discharge method: Optional hydraulic discharge machine can be used to press out from the top or high viscosity gear pump can be used to extract from the bottom discharge port. The pump can be used for material reflux circulation.
j. Other systems: Depending on the needs of different material processes, condensation devices or other devices can also be installed.
Application industry and scope of application:
This equipment is widely used in the industrial production of high viscosity materials, paste and paste materials,such as MS sealant, adhesive, organic silicone, electronic silicone, potting glue, patch red glue, printing glue, silicone sealant, glass glue, building structure glue, dry hanging glue, marble glue, AB two-component sealant, automotive sealant, thermal grease, lamp sealant, lubricating grease, ink, color paste and other high-viscosity materials, paste and pasty materials and other products.